

If flow is between these limits, perform calibration again, average results, and record orifice number and flow rate. (h) Calculate the flow rate and compare against the flow of 7.4☐.2 liters/minute. (2) Elapsed time, start and finish (at least two minutes) (1) Wet test meter reading, start and finish (g) Record the following on calibration data sheets: (f) Check the vacuum gauge on the pump to insure that the pressure drop across the orifice exceeds 17 inches of mercury
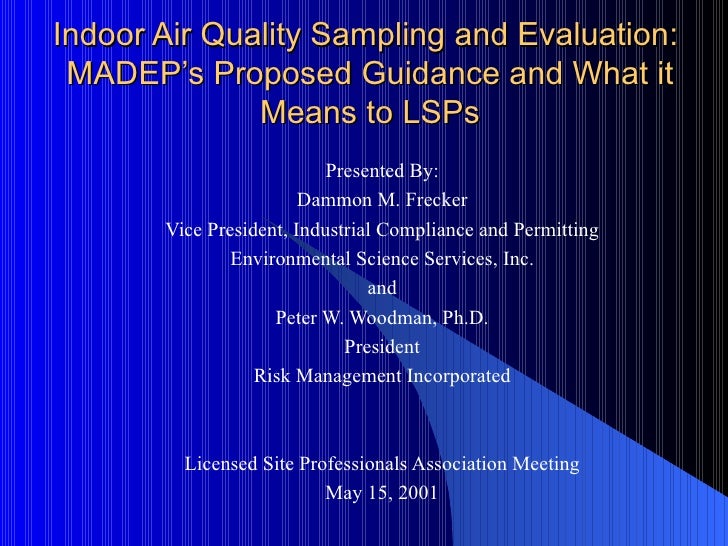
(e) Operate the system for ten minutes before starting the calibration If the pressure drop is greater than 1.0, disconnect and check the system
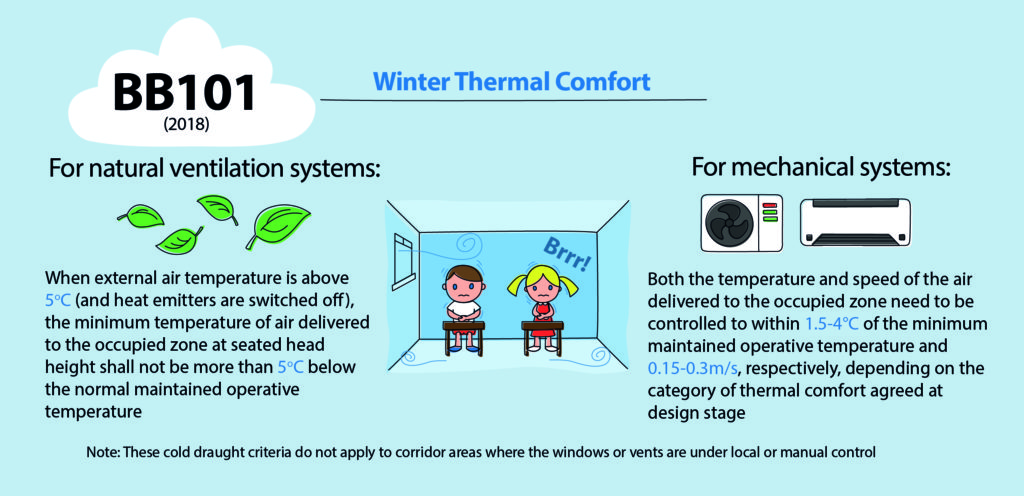
The pointer on the meter should run clockwise and a pressure drop of not more than 1.0 inch of water indicated. (d) Connect the wet test meter to the train. (c) Assemble the calibration sampling train (b) Place the polyvinyl chloride membrane filter in the filter cassette Run the meter for 30 minutes before calibration warmer than room temperature of till point.
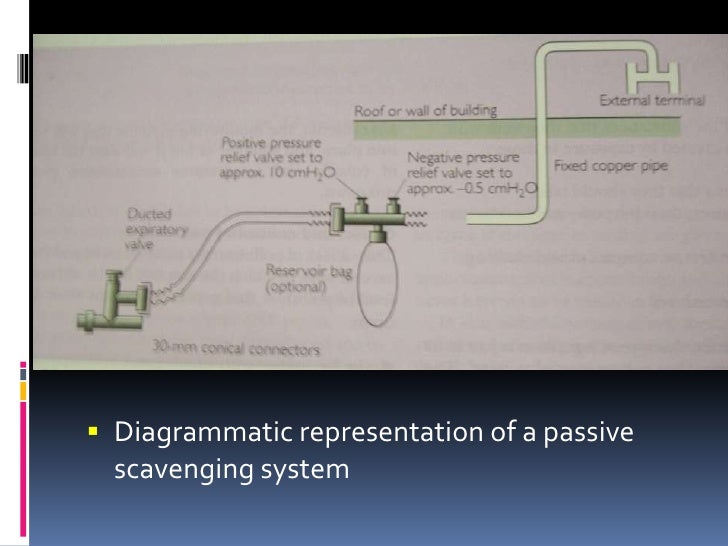
Check the water level which should just touch the calibration point at the left side of the meter. If another calibration device is selected, equivalent procedures should be used: Instructions for calibration with the wet test meter follow. The primary standard, such as a spirometer or other standard calibrating instruments such as a wet test meter or a large bubble meter or dry gas meter, should be used. The samplers should be calibrated in the laboratory both before they are used in the field and after they have been used to collect a large number of field samples. Samplers shall be calibrated when first received from the factory, after repair, and after receiving any abuse. (e) Monitoring equipment for use in Class III hazardous locations must be approved for use in such locations, in accordance with the requirements of the OSHA electrical standards in subpart S of part 1910. A balance sensitive to 10 micrograms should be used. A support pad, commonly called a backup pad, should be used under the filter membrane in the field monitor cassette. The membrane filters used should be polyvinyl chloride with a 5-um pore size and 37-mm diameter. Care must be exercised to insure that an adequate seal exists between elements of the cassette. A three-piece cassette constructed of polystyrene designed to hold a 37-mm diameter filter should be used. The pumps should be monitored during sampling. The samplers should be cleaned prior to sampling. It should operate at a flow rate of 7.4☐.2 liters/minute. The instrument selected for monitoring is the Lumsden-Lynch vertical elutriator. Summation of hours spent in each location and the dust concentration in that location.Ī time-weighted average concentration should be computed for each worker and properly logged and maintained on file for review. The daily time-weighted average (TWA) exposure of each worker can then be determined by using the following formula: Samples in each work area should be gathered simultaneously or sequentially during a normal operating period. In order to avoid filter overloading, sampling time may be shortened when sampling in dusty areas. Sufficient number of 6-hour area samples in each distinct work area of the plant should be collected at locations which provide representative samples of air to which the worker is exposed. The sampling procedures must be designed so that samples of the actual dust concentrations are collected accurately and consistently and reflect the concentrations of dust at the place and time of sampling. Appendix A to § 1910.1043 - Air Sampling and Analytical Procedures for Determining Concentrations of Cotton Dust
